The high cost of common ISO 9001 mistakes (and how to avoid them)
July 15, 2025
Effective quality management is critical for any organization. It builds customer trust, ensures compliance, and provides a competitive advantage. The ISO 9001 Quality Management System (QMS) standard offers a globally recognized framework for achieving consistent quality and operational excellence.
In 2025, ISO 9001 remains highly relevant. Businesses face complex supply chains, rising customer expectations, rapid digital transformation, and growing demands for sustainability and cybersecurity. In this environment, a structured QMS provides essential guidance to streamline operations, enhance customer satisfaction, and strengthen organizational resilience.
However, many organizations encounter significant challenges during ISO 9001 implementation and maintenance. Common errors can undermine the QMS, resulting in reduced benefits, compliance problems, and resource waste. Understanding these prevalent mistakes is vital for successful quality management and avoiding their substantial costs.
12 Common ISO 9001 Mistakes
Implementing and maintaining an ISO 9001 Quality Management System requires careful attention to detail and a clear understanding of its principles. Organizations frequently encounter challenges that can delay their progress or compromise the system's effectiveness.
Here are 12 prevalent errors to avoid:
- Lack of top management commitment: Without visible and sustained involvement from leadership, the QMS loses credibility. Management must allocate resources, define quality priorities, and reinforce accountability across functions.
- Inadequate scope definition: A scope that’s too broad adds complexity; too narrow, and it omits essential processes. The scope must accurately reflect operations relevant to quality performance and conformity.
- Over-documentation and bureaucracy: Many organizations produce excessive, redundant documentation that overwhelms users and clutters the QMS. At the same time, missing, obsolete, or inconsistent documents lead to audit findings and process failures. Overly complex procedures create resistance and reduce compliance. ISO 9001 requires lean, accurate, and controlled documentation that supports actual process execution.
- Failure to integrate the QMS into business operations: A common mistake is designing a QMS that exists separately from operational workflows. When quality requirements are added on top of existing processes rather than embedded into them, staff disengage, and compliance weakens. Integration must begin at the design stage, aligning the QMS with how work is actually performed.
- Weak internal auditing practices: Audits that are skipped or performed without depth fail to identify real issues. Audits must be risk-based, properly planned, and followed by corrective actions.
- Neglecting risk and data-driven decision-making: ISO 9001 emphasizes risk-based thinking and performance monitoring as foundational to planning and improvement. Common failures include treating risk as a formality, ignoring operational data, or failing to link KPIs to objectives. Organizations must proactively assess risks and use data to identify trends, prioritize actions, and inform decisions.
- Ineffective corrective actions: Addressing symptoms instead of root causes results in recurring problems. Corrective actions must include root cause analysis, implementation, and verification of effectiveness.
- Poor communication and awareness: Employees disengage when they don’t understand the QMS or its relevance to their role. Clear, ongoing communication and targeted training are essential.
- Ignoring customer feedback: the QMS always places a strong emphasis on customer satisfaction above all. A significant error is failing to systematically collect, analyze, and act upon customer feedback. This includes both positive and negative input, which provides invaluable insights for product, service, and process improvements.
- Treating certification as the end goal: Certification is a milestone, not the endpoint. Remember that the core principle of the standard is continuous improvement and without continued commitment, the QMS stagnates and its value declines over time. True value comes from ongoing focus on improvement and growth.
- Resistance to change: QMS implementation often meets resistance from staff used to informal systems. Change management and employee involvement are critical for adoption.
- Inadequate supplier management: The quality of an organization's products or services often depends heavily on its external providers. A common error is failing to establish robust controls for suppliers, neglecting to clearly define requirements for them, or not consistently monitoring their performance. This oversight can lead to issues with incoming materials or services, directly impacting the final quality of what the organization delivers and causing disruptions in the supply chain.
12 Common ISO 9001 Mistakes
Mistakes in ISO 9001 implementation and maintenance often carry both tangible and hidden costs. Beyond audit findings, they can disrupt operations, reduce customer satisfaction, and impact revenue. The table below outlines common errors, and the consequences organizations face when these issues are not addressed.
ISO 9001 error | Potential Cost | Example |
---|---|---|
Lack of top management commitment | Discontinued strategy, poor resource allocation | Objectives set but not backed with funding or assigned ownership |
Inadequate scope definition | Gaps in process coverage, audit delays, and certification risks | Excluded service units result in partial and noncompliant QMS scope |
Documentation issues | Audit nonconformities, inefficiency, outdated information, staff frustration | Teams using obsolete work instructions during an audit |
Failure to integrate QMS in operations | Redundant systems, low adoption, staff resistance | QMS ignored during production planning and performance reviews |
Weak internal audits | Undetected nonconformities, failed surveillance audits | Recurring issues missed in consecutive internal audit cycles |
Neglecting risk and data analysis | Reactive decisions, poor prioritization, missed trends | No KPIs reviewed in management meetings; risks addressed only after failure |
Ineffective corrective actions | Repeated issues, audit penalties, loss of credibility | Same nonconformity reported over multiple audits due to superficial fixes |
Poor communication and awareness | Inconsistent application, disengagement, change resistance | Staff unaware of revised quality procedures impacting their responsibilities |
Ignoring customer feedback | Missed improvements, declining satisfaction, lost contracts | Complaints ignored, resulting in contract termination by a major client |
Certification as the end goal | System stagnation, noncompliance, failed re-certification | No QMS updates after initial audit; readiness lost by next surveillance |
Resistance to change | Implementation delays, non-use of QMS elements | Employees bypass new processes using informal, undocumented methods |
Inadequate supplier management | Product defects, supply chain interruptions | Underperforming supplier not addressed until repeated failures escalate |
ISO 9001 Success Checklist: What to do Instead
Avoiding costly ISO 9001 errors requires a consistent, system-wide action. This checklist summarizes the key actions that support successful implementation, audit readiness, and long-term value.
Action | Benefit |
---|---|
Secure genuine top management engagement: Involve leadership in planning, reviews, and resource allocation. Communicate commitment and align quality objectives with business goals | Ensures strategic alignment, visible support, and clear accountability |
Define a relevant and realistic scope: Identify processes, products, and services within QMS boundaries. Align scope with actual operations and document it clearly | Avoids gaps or overreach and ensures audit readiness |
Streamline and control documentation: Create lean, accurate documents. Use clear process maps. Implement version control and ensure accessibility | Reduces inefficiency, audit findings, and user frustration |
Integrate QMS into core operations: Embed quality into real workflows. Align the QMS with how work is actually done | Improves adoption, reduces duplication, and supports efficiency |
Conduct effective internal audits: Plan audits based on risk and performance. Use trained auditors and ensure timely corrective action | Detects issues early and supports continual improvement |
Use risk and performance data: Identify risks and opportunities. Track KPIs. Use insights to guide priorities and decisions | Enables proactive management and evidence-based actions |
Apply effective corrective actions: Conduct root cause analysis, implement targeted actions, and verify results | Prevents recurrence and builds trust in the QMS |
Communicate and build awareness: Share QMS expectations. Train staff. Encourage feedback and involvement | Improves consistency, engagement, and ownership |
Act on customer feedback: Collect, analyze, and respond to feedback systematically | Drives improvements and increases satisfaction |
Commit to continual improvement: Apply PDCA. Review performance. Set new goals and maintain QMS momentum | Keeps the system relevant and evolving |
Manage suppliers proactively: Define criteria, monitor performance, and address nonconformities | Strengthens supply chain quality and reliability |
Avoidable vs. Inevitable Mistakes
Some mistakes in an ISO 9001 QMS are entirely preventable with proactive planning and commitment, while others are a more natural part of the learning and improvement process. Distinguishing between avoidable and inevitable mistakes helps organizations focus resources where they matter most and recognize early missteps as opportunities for improvement.
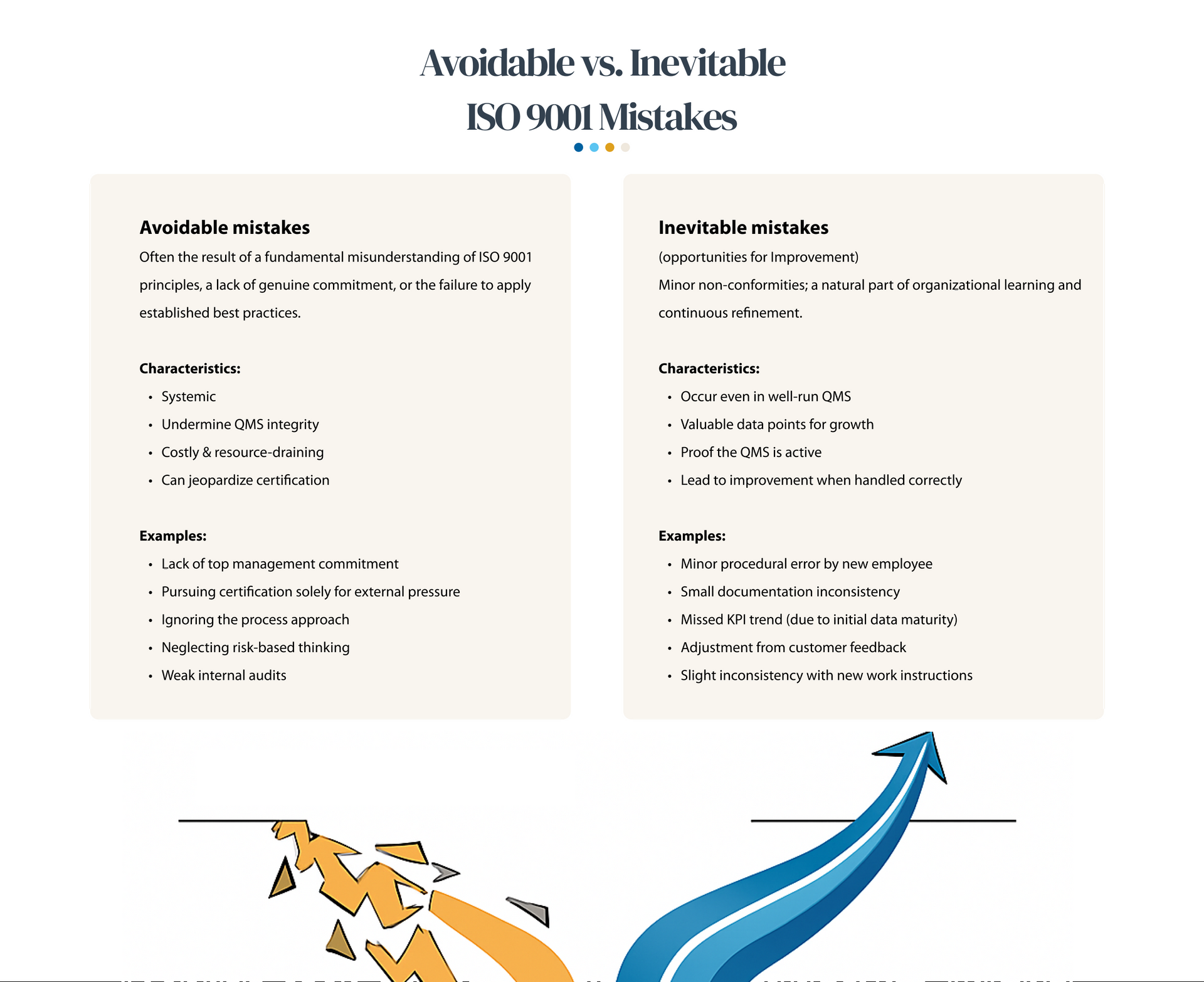
Avoidable mistakes are errors stemming from fundamental misunderstanding, lack of commitment, or failure to apply best practices. Avoidable mistakes are characterized as systemic that undermine QMS integrity and are costly and resource-draining. These kinds of errors can easily jeopardize certification. An example of an avoidable mistake is a weak internal audit.
Inevitable mistakes are minor non-conformities and are a natural part of organizational learning and continuous refinement.
Inevitable mistakes can happen to organization, even well-run QMS, and are often seen as valuable data points for growth. These mistakes often prove that an organization's QMS is active and well prepared. An example of an inevitable mistake would be minor procedural error by new employee.
Proactive management prevents avoidable errors. Effective QMS processes turn inevitable issues into improvement.
Real-World Lessons: Common Errors by Industry
Industry | Common Error | Why it Happens | Lesson Learned |
---|---|---|---|
Manufacturing | Outdated or uncontrolled work instructions | Informal updates, lack of document control on the shop floor | Use digital document control and conduct routine floor audits |
Inadequate calibration records for critical equipment | Missing schedules or incomplete traceability | Establish and monitor a calibration program with audit-ready documentation | |
IT/Service | QMS not aligned with agile development processes | ISO 9001 seen as too rigid for iterative work | Integrate QMS tasks into sprint planning and ticket workflows |
Poor customer complaint handling | Feedback treated as isolated incidents | Treat feedback as a formal input into service and process improvement | |
Healthcare | Procedures not aligned with actual clinical practices | Staff follow routine practices not reflected in documents | Review documents with staff to ensure real-world accuracy |
Administrative functions excluded from audits | Focus limited to clinical or regulated departments | Expand internal audit scope to include admin and support functions | |
Construction | Uncontrolled changes during project execution | Field changes not documented or reflected in quality records | Reinforce change control discipline at site level and integrate with project plans |
Weak subcontractor qualification and monitoring | No clear criteria or performance tracking | Set supplier requirements and maintain performance logs |
Navigating ISO 9001 is essential for organizations, but common mistakes can significantly diminish its value. Understanding these pitfalls and their costs is the crucial first step toward an effective Quality Management System.
A functional ISO 9001 QMS is a dynamic tool for operational excellence, continuous improvement, and sustained business success. By implementing the proactive strategies outlined in our checklist, organizations can strengthen their QMS, ensuring it contributes genuine value and drives consistent quality outcomes.
Preventing these errors and fostering a culture of quality requires specialized knowledge and practical skills. Safeshield provides accredited ISO 9001 training programs designed to equip professionals with the expertise needed to implement, manage, and audit robust quality systems. Whether you are building foundational knowledge with our ISO 9001 Foundation course, mastering implementation through our ISO 9001 Lead Implementer training, or becoming an expert auditor with our ISO 9001 Lead Auditor training, our programs offer the tools to avoid common pitfalls and achieve lasting excellence.
Explore Safeshield's flexible self-study, online learning and instructor-led training opportunities, including those available in Ontario, Canada.
Share this article